Bilah turbin
Bilah turbin adalah airfoil radial yang dipasang di tepi cakram turbin dan menghasilkan gaya tangensial yang memutar rotor turbin. Setiap cakram turbin memiliki banyak bilah. Dengan demikian, bilah turbin digunakan dalam mesin turbin gas dan turbin uap. Bilah turbin bertanggung jawab untuk mengekstraksi energi dari gas bersuhu tinggi dan bertekanan tinggi yang dihasilkan oleh pembakar. Bilah turbin sering kali menjadi komponen pembatas turbin gas. Untuk bertahan hidup di lingkungan yang sulit ini, bilah turbin sering kali menggunakan material eksotis seperti superalloy dan berbagai metode pendinginan yang dapat dikategorikan sebagai pendinginan internal dan eksternal, dan pelapis penghalang termal. Kelelahan bilah merupakan sumber utama kegagalan pada turbin uap dan turbin gas. Kelelahan disebabkan oleh tegangan yang disebabkan oleh getaran dan resonansi dalam rentang operasi mesin. Untuk melindungi bilah dari tegangan dinamis yang tinggi ini, peredam gesekan digunakan.[1][2][3][4][5] and thermal barrier coatings.[6][7][8]
Bilah turbin angin dan turbin air dirancang untuk beroperasi dalam kondisi yang berbeda, yang biasanya melibatkan kecepatan putaran dan suhu yang lebih rendah.
Perkenalan





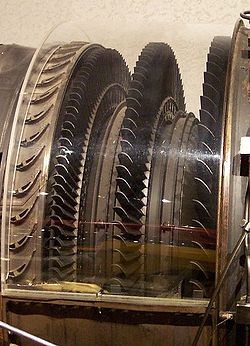






Pada mesin turbin gas, satu tahap turbin terdiri dari cakram berputar yang menampung banyak bilah turbin dan cincin stasioner dari bilah pemandu nosel di depan bilah. Turbin dihubungkan ke kompresor menggunakan poros (rakitan berputar lengkap yang terkadang disebut "spul"). Udara dikompresi, meningkatkan tekanan dan suhu, saat melewati kompresor. Suhu kemudian ditingkatkan dengan pembakaran bahan bakar di dalam pembakar yang terletak di antara kompresor dan turbin. Gas bersuhu tinggi dan bertekanan tinggi kemudian melewati turbin. Tahap turbin mengekstrak energi dari aliran ini, menurunkan tekanan dan suhu gas dan mentransfer energi kinetik ke kompresor. Cara kerja turbin mirip dengan cara kerja kompresor, hanya saja secara terbalik, sejauh menyangkut pertukaran energi antara gas dan mesin, misalnya. Ada hubungan langsung antara seberapa banyak perubahan suhu gas (peningkatan kompresor, penurunan turbin) dan masukan daya poros (kompresor) atau keluaran (turbin).[9][10][11]
Untuk mesin turbofan jumlah tingkat turbin yang diperlukan untuk menggerakkan kipas meningkat dengan rasio bypass kecuali kecepatan turbin dapat ditingkatkan dengan menambahkan kotak roda gigi antara turbin dan kipas, dalam hal ini lebih sedikit tingkat yang diperlukan. Jumlah tingkat turbin dapat memiliki efek besar pada bagaimana bilah turbin dirancang untuk setiap tingkat. Banyak mesin turbin gas adalah desain kumparan kembar, yang berarti ada kumparan bertekanan tinggi dan kumparan bertekanan rendah. Turbin gas lainnya menggunakan tiga kumparan, menambahkan kumparan bertekanan menengah antara kumparan bertekanan tinggi dan rendah. Turbin bertekanan tinggi terkena udara terpanas dan bertekanan tertinggi, dan turbin bertekanan rendah terkena udara yang lebih dingin dan bertekanan lebih rendah. Perbedaan kondisi mengarah pada desain bilah turbin bertekanan tinggi dan bertekanan rendah yang secara signifikan berbeda dalam pilihan material dan pendinginan meskipun prinsip aerodinamis dan termodinamikanya sama. Dalam kondisi operasi yang berat di dalam turbin gas dan uap, bilah turbin menghadapi suhu tinggi, tekanan tinggi, dan kemungkinan getaran tinggi. Bilah turbin uap merupakan komponen penting dalam pembangkit listrik yang mengubah gerakan linier uap bersuhu tinggi dan bertekanan tinggi yang mengalir menuruni gradien tekanan menjadi gerakan putar poros turbin.
Desain bilah
Kompresor aliran aksial transonik banyak digunakan dalam mesin pesawat karena memberikan rasio tekanan tinggi per tahap. Efisiensi tinggi merupakan salah satu target penting kompresor aksial transonik karena bermanfaat untuk meningkatkan efisiensi bahan bakar mesin dan menghasilkan biaya bahan bakar yang lebih rendah serta jarak terbang yang lebih jauh. Di antara faktor-faktor yang memengaruhi, desain bilah merupakan faktor penting yang memiliki pengaruh signifikan terhadap efisiensi kompresor aksial transonik. Dalam prosedur desain kompresor transonik, bilah dirancang dengan menggunakan metode desain geometri dengan kriteria desain aerodinamis terkait atau dikombinasikan dengan algoritma optimasi. Oleh karena itu, metode desain geometri yang fleksibel dan praktis, yang memiliki ruang desain yang cukup untuk menampung bentuk bilah dengan kinerja aerodinamis yang sangat baik, berguna untuk meningkatkan efisiensi kompresor transonik.
Bilah kompresor transonik modern terdiri dari beberapa elemen bilah dua dimensi, yang disebut sebagai airfoil, di sepanjang garis susun radial. Geometri airfoil memiliki pengaruh penting terhadap kinerja aerodinamis bilah kompresor dengan memengaruhi aliran permukaan aliran S1. Airfoil Double Circular Arc (DCA) dan airfoil Multi Circular Arc (MCA) yang dikembangkan lebih lanjut adalah airfoil yang paling banyak digunakan dalam desain tahap awal kompresor aksial transonik. MCA telah meningkatkan fleksibilitas desain dibandingkan dengan DCA dengan menggabungkan beberapa busur melingkar dengan radius kelengkungan yang berbeda, membentuk permukaan airfoil untuk mengubah defleksi guna mengendalikan kekuatan guncangan dengan lebih baik, yang menghasilkan efisiensi yang lebih tinggi untuk bilangan Mach yang lebih besar dari 1,3
Rotor dan stator




Turbin merupakan jantung dari setiap mesin jet dengan tugas utamanya adalah menggerakkan kompresor. Seperti yang dijelaskan sebelumnya, tanpa kompresor, tidak akan ada kerja mekanis yang dilakukan pada fluida sebelum pembakaran dan daya dorong yang dihasilkan hanya akan menjadi fungsi dari energi kimia yang tersimpan dalam bahan bakar. Gas hasil pembakaran panas yang masuk ke turbin langsung setelah ruang pembakaran diekspansikan melalui serangkaian bilah rotor dan stator, yang dikenal sebagai tahap, mirip dengan kompresor. Dalam kasus turbin, fluida diekspansikan untuk mengekstraksi kerja yang berguna dan oleh karena itu tekanan fluida turun di setiap tahap turbin. Karena fluida tidak bekerja melawan gradien tekanan yang merugikan (meningkat), pemisahan lapisan batas di atas aerofoil bilah turbin tidak terlalu penting sehingga bilah turbin dapat memiliki sudut serang yang jauh lebih agresif terhadap aliran. Akibatnya, rasio tekanan di seluruh tahap turbin dapat jauh lebih tinggi daripada di seluruh tahap kompresor dan cukup umum bagi satu tahap turbin untuk menggerakkan enam atau tujuh tahap kompresor. Jumlah daya yang dapat diekstraksi dari tahap turbin sangat besar dan satu bilah turbin (bukan seluruh rotor bilah) dapat menghasilkan hingga 250 bhp. Penggerak terbesar di balik kemajuan teknologi turbin sejak mesin pertama Whittle pada tahun 1930-an adalah pengembangan metode pendinginan canggih dan penggunaan paduan suhu tinggi.
Mirip dengan kompresor, turbin aksial pada sebagian besar pesawat jet modern lebih efisien daripada turbin radial pada laju aliran yang lebih tinggi. Namun, turbin radial masih digunakan pada pesawat modern untuk unit daya tambahan. Contohnya turbin aksial tiga tahap poros tunggal, yaitu tiga tahap turbin menggerakkan semua tahap kompresor melalui satu poros.
Gas panas yang keluar dari ruang pembakaran dan mengenai baris pertama bilah pemandu nosel yang mengubah aliran menjadi bilah turbin yang berputar pada sudut optimal untuk mengekstraksi jumlah kerja terbanyak. Setiap tahap bilah dan bilah memperluas aliran sehingga mengakibatkan penurunan entalpi (jumlah total energi dalam gas pembakaran) dan pemindahan kerja dari fluida ke turbin. Untuk mesin jet sederhana, kinerja keseluruhan mesin ditingkatkan secara lebih efektif dengan mengembangkan tahap kompresor. Pada mesin turbofan by-pass besar, desain aerodinamis turbin sangat penting. Segitiga kecepatan untuk aliran yang melewati satu tahap turbin. Baris turbin yang terpisah biasanya ditempatkan sangat berdekatan, sekitar 20% dari tali bilah, dan kecepatan tangensial bilah rotor w*r ( w adalah kecepatan putar dan r adalah jari-jari bilah) mendekati kecepatan suara lokal.
Fungsi utama stator bukanlah untuk melakukan kerja tetapi untuk menambahkan pusaran pada aliran guna mengubah sebagian panas internalnya menjadi energi kinetik. Rotor turbin kemudian mengekstraksi kerja dari aliran dengan menghilangkan energi kinetik yang terkait dengan kecepatan pusaran. Dalam kerangka acuan global mesin, aliran ke stator dan rotor sangat tidak stabil dan sangat rumit. Namun, dalam kerangka acuan yang dipasang pada bilah yang berputar, aliran tersebut dapat diasumsikan cukup stabil dengan akurasi yang memadai. Untuk baris pertama stator (atau bilah pemandu nosel), aliran tersebut mengenai arah aliran aksial yang sejajar dan akibatnya diputar melalui sudut β b terhadap arah aksial oleh stator. Dengan demikian, aliran meninggalkan stator pada kecepatan V b terhadap stator yang setara dengan kecepatan V' b pada sudut β' b terhadap bilah yang berputar. Pada kondisi desain optimal, β' b sama dengan sudut bilah rotor. V' c dan β' c masing-masing adalah kecepatan keluar relatif dan sudut bilah, sehingga sudut putar sama dengan β' b – β' c . Parameter desain yang penting untuk kinerja turbin adalah koefisien bilah φ, yang merupakan rasio penurunan suhu total (yang proporsional dengan kerja yang dilakukan) di seluruh tahap dibagi dengan energi kinetik rotor.
Efisiensi tinggi dicapai dengan penurunan suhu yang lebih rendah per tahap dan karenanya nilai φ yang lebih kecil dan sudut putar yang lebih rendah β' b – β' c . Namun nilai φ yang besar diperlukan untuk mengurangi jumlah tahap dan menjaga bobot mesin tetap rendah. Akibatnya, kompromi harus dilakukan antara mengoptimalkan efisiensi termodinamika dan bobot.
Jika tekanan tinggi dari fluida yang keluar dari ruang pembakaran diekspansi dalam satu tahap, kecepatan yang sangat tinggi mendekati 1500 m/s akan dihasilkan, yang karena kerugian yang terkait dengan gelombang kejut supersonik, tidak mungkin digunakan secara efisien. Oleh karena itu, tahap turbin membuat serangkaian ekspansi tambahan yang menghasilkan aliran tepat di atas kecepatan suara lokal, yang, seperti yang ditunjukkan oleh segitiga kecepatan, tampaknya berkurang saat masuk ke tahap berikutnya sebagai akibat dari perubahan kerangka acuan. Dengan demikian, segitiga kecepatan menunjukkan bahwa kecepatan yang meninggalkan stator V b tinggi dalam kerangka acuan yang sesuai dengan stator tetapi jauh lebih rendah jika dilihat di pintu masuk rotor V' b. Demikian pula kecepatan yang meninggalkan rotor tinggi dalam kerangka acuan relatifnya V' c. tetapi lebih rendah dalam kerangka absolut yang sesuai dengan stator V c. Dengan demikian, setiap baris turbin menerima aliran yang hampir aksial ke bawah mesin dan memutarnya ke arah tangensial sehingga mengurangi luas aliran penampang efektif, yang, dengan konservasi momentum, harus menghasilkan peningkatan kecepatan fluida.
Tekanan Turbin
Bilah-bilah saluran masuk turbin tahap pertama adalah yang paling mungkin menentukan umur mesin karena bilah-bilah tersebut bekerja pada suhu fluida tertinggi, kecepatan putar tertinggi, dan beban aerodinamis tertinggi. Tegangan pada bilah rotor juga membatasi tinggi bilah yang diizinkan dan area aliran anulus. Tegangan mekanis kotor muncul dari tegangan sentrifugal turbin yang berputar dan momen lentur yang bekerja oleh gas yang mengalir, yang sayangnya keduanya maksimum pada akar bilah. Masalah tegangan akar sentrifugal sebelumnya telah dibahas untuk bilah kompresor. Bilah-bilah turbin tentu saja disetel sedemikian rupa sehingga tidak ada frekuensi alaminya yang bertepatan dengan frekuensi eksitasi putar atau fluida apa pun untuk mencegah perilaku resonansi. Turbin gas menghasilkan daya spesifik yang lebih tinggi dan dengan demikian efisiensi karena suhu masuk turbin (TET) gas yang keluar dari ruang bakar meningkat. Tentu saja TET dibatasi oleh metalurgi bahan bilah turbin. TET meningkat dari sekitar 800°C pada tahun 1940 menjadi 1500°C pada mesin Rolls-Royce Trent tahun 1994. Perkembangan ini sebagian disebabkan oleh bahan yang lebih baik, tetapi yang lebih penting adalah melalui penyaluran udara kompresor dingin untuk mendinginkan bilah turbin.
Dalam lingkungan suhu tinggi ini, masa pakai bilah turbin dibatasi oleh creep, yang merupakan perpanjangan material secara terus-menerus dan bertahap di bawah beban konstan dari waktu ke waktu. Selain mendistorsi dimensi fisik dan dengan demikian mengurangi kinerja mesin, tegangan creep yang diinduksi memperburuk tegangan operasi sentrifugal dan karenanya akan menyebabkan kegagalan material sebelum waktunya. Dalam suhu sekitar, creep sering kali hanya menjadi faktor untuk elastomer dan plastik lainnya, tetapi pada suhu yang lebih tinggi, efeknya menjadi semakin jelas untuk logam juga. Aturan praktisnya adalah bahwa masa pakai bilah berkurang setengahnya (untuk bahan bilah dan teknologi pendinginan tertentu) untuk setiap kenaikan suhu logam sebesar 10°C. Pada masa-masa awal teknologi turbin, bilah ditempa tetapi kemudian dituang untuk kinerja suhu tinggi yang lebih baik. Kemudian ditemukan bahwa dengan memanjangkan kristal logam di sepanjang arah bentang, menciptakan apa yang disebut bilah yang dipadatkan secara terarah, menghasilkan peningkatan lebih lanjut dalam kinerja creep. Teknik standar untuk bilah berkinerja tinggi adalah dengan menuang bilah dari kristal tunggal. Logam dapat berubah bentuk karena adanya kristal terpisah yang bergeser di sepanjang batas butir, sehingga menghilangkan seluruh batas butir akan menghasilkan peningkatan besar dalam menahan deformasi mulur.
Paduan yang umum digunakan untuk bilah turbin saat ini adalah Inconel, paduan berbasis nikel yang mengandung 13% kromium, 6% besi, dengan sedikit mangan, silikon, dan tembaga. Kemajuan metalurgi ini menghasilkan beberapa peningkatan dalam meningkatkan efisiensi TET dan turbin. Teknologi lain yang sangat menarik dan rumit adalah teknik pendinginan bilah.
Kompresor Aliran Sentrifugal
Kompresor aliran sentrifugal terdiri dari impeller (rotor), diffuser (stator), dan manifold kompresor. Kompresor sentrifugal memiliki kenaikan tekanan tinggi per tahap yang dapat mencapai sekitar 8:1. Umumnya kompresor sentrifugal dibatasi hingga dua tahap karena masalah efisiensi. Dua elemen fungsional utama adalah impeller dan diffuser. Meskipun diffuser adalah unit terpisah dan ditempatkan di dalam dan dibaut ke manifold, seluruh rakitan (diffuser dan manifold) sering disebut sebagai diffuser. Untuk klarifikasi selama pengenalan kompresor, unit-unit tersebut diperlakukan secara individual. Impeller biasanya terbuat dari paduan aluminium tempa, diberi perlakuan panas, dikerjakan dengan mesin, dan dihaluskan untuk pembatasan aliran dan turbulensi minimum.
Pada sebagian besar tipe, impeller dibuat dari satu tempa.Impeller, yang fungsinya adalah untuk mengambil dan mempercepat udara keluar ke diffuser, dapat berupa salah satu dari dua tipe—entri tunggal atau entri ganda. Perbedaan utama antara kedua tipe impeller adalah ukuran dan susunan saluran. Tipe entri ganda memiliki diameter yang lebih kecil, tetapi biasanya dioperasikan pada kecepatan putaran yang lebih tinggi untuk memastikan aliran udara yang cukup. Impeller entri tunggal, memungkinkan saluran yang mudah langsung ke mata impeller (baling-baling inducer) dibandingkan dengan saluran yang lebih rumit yang diperlukan untuk mencapai sisi belakang tipe entri ganda. Meskipun sedikit lebih efisien dalam menerima udara, impeller entri tunggal harus berdiameter besar untuk mengalirkan jumlah udara yang sama dengan tipe entri ganda. Ini, tentu saja, meningkatkan diameter keseluruhan mesin.
Termasuk dalam saluran untuk mesin kompresor entri ganda adalah ruang plenum. Ruang ini diperlukan untuk kompresor entri ganda karena udara harus masuk ke mesin pada sudut yang hampir tegak lurus dengan sumbu mesin. Oleh karena itu, untuk memberikan aliran positif, udara harus mengelilingi kompresor mesin pada tekanan positif sebelum memasuki kompresor. Termasuk dalam beberapa instalasi sebagai bagian penting dari ruang plenum adalah pintu pemasukan udara tambahan (pintu tiup). Pintu tiup ini memasukkan udara ke kompartemen mesin selama operasi darat, ketika kebutuhan udara untuk mesin melebihi aliran udara melalui saluran masuk. Pintu-pintu tersebut ditahan tertutup oleh aksi pegas saat mesin tidak beroperasi. Namun, selama operasi, pintu terbuka secara otomatis setiap kali tekanan kompartemen mesin turun di bawah tekanan atmosfer. Selama lepas landas dan terbang, tekanan udara ram di kompartemen mesin membantu pegas dalam menahan pintu agar tetap tertutup.
Diffuser adalah ruang melingkar yang dilengkapi dengan sejumlah bilah yang membentuk serangkaian saluran divergen ke dalam manifold. Baling-baling diffuser mengarahkan aliran udara dari impeller ke manifold pada sudut yang dirancang untuk mempertahankan jumlah energi maksimum yang diberikan oleh impeller. Baling-baling tersebut juga mengalirkan udara ke manifold pada kecepatan dan tekanan yang memuaskan untuk digunakan di ruang pembakaran.
Manifold kompresor mengalihkan aliran udara dari diffuser, yang merupakan bagian integral dari manifold, ke dalam ruang pembakaran. Manifold memiliki satu port outlet untuk setiap ruang sehingga udara terbagi secara merata. Siku outlet kompresor dibaut ke setiap port outlet. Outlet udara ini dibuat dalam bentuk saluran dan dikenal dengan berbagai nama, seperti saluran outlet udara, siku outlet, atau saluran masuk ruang pembakaran. Terlepas dari terminologi yang digunakan, saluran outlet ini melakukan bagian yang sangat penting dari proses difusi; yaitu, mereka mengubah arah radial aliran udara ke arah aksial, di mana proses difusi selesai setelah belokan. Untuk membantu siku melakukan fungsi ini secara efisien, bilah putar (baling-baling kaskade) terkadang dipasang di dalam siku. Bilah-baling ini mengurangi kehilangan tekanan udara dengan menghadirkan permukaan putar yang halus.
Kompresor Aliran Aksial
Kompresor aliran aksial memiliki dua elemen utama: rotor dan stator. Rotor memiliki bilah yang terpasang pada spindel. Bilah-bilah ini mendorong udara ke belakang dengan cara yang sama seperti baling-baling karena sudut dan kontur airfoilnya. Rotor, yang berputar dengan kecepatan tinggi, mengambil udara di saluran masuk kompresor dan mendorongnya melalui serangkaian tahap. Dari saluran masuk hingga keluar, udara mengalir sepanjang jalur aksial dan dikompresi dengan rasio sekitar 1,25:1 per tahap. Aksi rotor meningkatkan kompresi udara di setiap tahap dan mempercepatnya ke belakang melalui beberapa tahap. Dengan peningkatan kecepatan ini, energi ditransfer dari kompresor ke udara dalam bentuk energi kecepatan. Bilah stator bertindak sebagai penyebar di setiap tahap, sebagian mengubah kecepatan tinggi menjadi tekanan. Setiap pasangan bilah rotor dan stator yang berurutan membentuk tahap tekanan. Jumlah baris bilah (tahap) ditentukan oleh jumlah udara dan kenaikan tekanan total yang diperlukan. Rasio tekanan kompresor meningkat seiring dengan jumlah tahap kompresi. Sebagian besar mesin menggunakan hingga 16 tahap dan lebih.
Stator memiliki deretan bilah, yang pada gilirannya terpasang di dalam casing penutup. Bilah stator, yang diam, menonjol secara radial ke arah sumbu rotor dan pas di kedua sisi setiap tingkat bilah rotor. Dalam beberapa kasus, casing kompresor, tempat bilah stator dipasang, dibagi secara horizontal menjadi dua bagian. Baik bagian atas maupun bawah dapat dilepas untuk pemeriksaan atau perawatan bilah rotor dan stator.
Fungsi bilah stator adalah untuk menerima udara dari saluran masuk udara atau dari setiap tahap sebelumnya dan meningkatkan tekanan udara dan menyalurkannya ke tahap berikutnya pada kecepatan dan tekanan yang benar. Mereka juga mengendalikan arah udara ke setiap tahap rotor untuk mendapatkan efisiensi bilah kompresor semaksimal mungkin. Bilah rotor tahap pertama dapat didahului oleh rakitan bilah pemandu saluran masuk yang dapat tetap atau variabel.
Baling-baling pemandu mengarahkan aliran udara ke bilah rotor tahap pertama pada sudut yang tepat dan memberikan gerakan berputar pada udara yang memasuki kompresor. Praputaran ini, ke arah putaran mesin, meningkatkan karakteristik aerodinamis kompresor dengan mengurangi hambatan pada bilah rotor tahap pertama. Baling-baling pemandu saluran masuk adalah bilah baja melengkung yang biasanya dilas ke selubung baja bagian dalam dan luar.
Pada ujung pembuangan kompresor, bilah stator dibuat untuk meluruskan aliran udara guna menghilangkan turbulensi. Bilah-bilah ini disebut bilah pelurus atau rakitan bilah saluran keluar. Casing kompresor aliran aksial tidak hanya menopang bilah stator dan menyediakan dinding luar jalur aksial yang diikuti udara, tetapi juga menyediakan sarana untuk mengekstraksi udara kompresor untuk berbagai keperluan. Bilah stator biasanya terbuat dari baja dengan kualitas tahan korosi dan erosi. Cukup sering, bilah-bilah tersebut diselimuti (tertutup) oleh pita bahan yang sesuai untuk menyederhanakan masalah pengikatan. Baling-baling dilas ke dalam selubung, dan selubung luar diamankan ke dinding bagian dalam rumah kompresor dengan sekrup penahan radial.
Bilah rotor biasanya terbuat dari baja tahan karat dengan tahap akhir terbuat dari titanium. Desain pemasangan bilah ke pelek cakram rotor bervariasi, tetapi umumnya dipasang ke cakram dengan metode tipe bohlam atau pohon cemara. Bilah kemudian dikunci pada tempatnya dengan metode yang berbeda. Ujung bilah kompresor dikurangi ketebalannya dengan potongan, yang disebut profil bilah. Profil ini mencegah kerusakan serius pada bilah atau rumah jika bilah menyentuh rumah kompresor. Kondisi ini dapat terjadi jika bilah rotor menjadi terlalu longgar atau jika dukungan rotor berkurang karena bantalan yang tidak berfungsi dengan baik. Meskipun profil bilah sangat mengurangi kemungkinan tersebut, terkadang bilah dapat patah karena tekanan gesekan dan menyebabkan kerusakan yang cukup besar pada bilah kompresor dan rakitan bilah stator. Panjang bilah bervariasi dari pintu masuk hingga pembuangan karena ruang kerja melingkar (drum ke casing) berkurang secara progresif ke arah belakang oleh penurunan diameter casing. Fitur ini memberikan kecepatan yang cukup konstan melalui kompresor, yang membantu menjaga aliran udara tetap konstan.
Rotor memiliki konstruksi tipe drum atau tipe cakram. Rotor tipe drum terdiri dari cincin yang diberi flens agar pas satu dengan yang lain, di mana seluruh rakitan kemudian dapat disatukan oleh baut tembus. Jenis konstruksi ini memuaskan untuk kompresor kecepatan rendah di mana tegangan sentrifugal rendah. Rotor tipe cakram terdiri dari serangkaian cakram yang dibuat dari tempaan aluminium, menyusut di atas poros baja, dengan bilah rotor yang disambungkan ke tepi cakram. Metode konstruksi rotor lainnya adalah dengan membuat cakram dan poros dari tempaan aluminium tunggal, dan kemudian memasang poros baja di bagian depan dan belakang rakitan untuk menyediakan permukaan penyangga bantalan dan spline untuk menyambung poros turbin.
Kombinasi tahapan kompresor dan tahapan turbin pada poros umum adalah mesin yang disebut sebagai kumparan mesin. Poros umum disediakan dengan menggabungkan poros turbin dan kompresor dengan metode yang sesuai. Kumparan mesin didukung oleh bantalan, yang ditempatkan di rumah bantalan yang sesuai.
Seperti yang disebutkan sebelumnya, ada dua konfigurasi kompresor aksial yang saat ini digunakan: rotor/kumparan tunggal dan rotor/kumparan ganda, kadang-kadang disebut sebagai kumparan padat dan kumparan terpisah (dua kumparan, kumparan ganda).
Satu versi kompresor kumparan padat (satu kumparan) menggunakan bilah pemandu saluran masuk variabel. Selain itu, beberapa baris pertama bilah stator bervariasi. Perbedaan utama antara bilah pemandu saluran masuk variabel (VIGV) dan bilah stator variabel (VSV) adalah posisi mereka sehubungan dengan bilah rotor. VIGV berada di depan bilah rotor, dan VSV berada di belakang bilah rotor. Sudut bilah pemandu saluran masuk dan beberapa tahap pertama bilah stator dapat bervariasi. Selama pengoperasian, udara masuk ke bagian depan mesin dan diarahkan ke kompresor pada sudut yang tepat oleh pemandu saluran masuk variabel dan diarahkan oleh VSV. Udara dikompresi dan dipaksa masuk ke bagian pembakaran. Nosel bahan bakar yang memanjang ke setiap liner pembakaran mengatomisasi bahan bakar untuk pembakaran. Variabel-variabel ini dikontrol secara langsung terkait dengan jumlah daya yang harus dihasilkan mesin melalui posisi tuas daya.
Sebagian besar mesin turbofan adalah jenis kompresor split-spool. Sebagian besar mesin turbofan besar menggunakan kipas besar dengan beberapa tahap kompresi yang disebut spool tekanan rendah. Turbofan ini menggabungkan dua kompresor dengan turbin masing-masing dan poros penghubung, yang membentuk dua sistem rotor yang secara fisik independen. Banyak sistem rotor ganda memiliki rotor yang berputar ke arah yang berlawanan dan tanpa koneksi mekanis satu sama lain. Spool kedua, disebut sebagai spool tekanan tinggi dan merupakan kompresor untuk generator gas dan inti mesin, memasok udara ke bagian pembakaran mesin.
Keuntungan dan kerugian jenis kompresor
Keuntungan dan kerugian dari kedua jenis kompresor disertakan dalam daftar berikut. Meskipun setiap jenis memiliki kelebihan dan kekurangan, masing-masing memiliki kegunaannya sendiri berdasarkan jenis dan ukuran mesin.
Keuntungan kompresor aliran sentrifugal adalah:
- Kenaikan tekanan tinggi per tahap
- Efisiensi pada rentang kecepatan putaran yang lebar
- Mudah dibuat dan biaya rendah
- Berat badan rendah
- Persyaratan daya awal yang rendah.
Kerugian kompresor aliran sentrifugal adalah:
- Area frontalnya yang besar untuk aliran udara tertentu
- Kerugian dalam putaran antar tahapan
Keunggulan kompresor aliran aksial adalah:
- Efisiensi puncak tinggi
- Area frontal kecil untuk aliran udara tertentu
- Aliran langsung, memungkinkan efisiensi ram yang tinggi
- Peningkatan tekanan meningkat dengan meningkatnya jumlah tahapan, dengan kerugian yang dapat diabaikan
Kerugian kompresor aliran aksial adalah:
- Efisiensi yang baik hanya pada rentang kecepatan putaran yang sempit
- Kesulitan pembuatan dan biaya tinggi
- Berat yang relatif tinggi
- Persyaratan daya awal yang tinggi (sebagian diatasi oleh kompresor split)
Perbedaan kipas turbin dan kipas kompresor
Bilah kompresor umumnya tipis dan lurus, dan menyerupai sayap persegi panjang kecil dengan ketebalan camber rendah. Bilah turbin lebih melengkung, sering kali berbentuk hampir "U" (seperti yang terlihat di sini). Pada mesin yang sangat besar dan baru, di mana efisiensi sangat penting, bilah turbin sering kali penuh dengan lubang kecil:
Untuk membedakan antara tahap tekanan tinggi dan tekanan rendah (kompresor atau turbin), panjang bilah dan torsinya (yaitu seberapa banyak profil aerodinamis berputar di sekitar sumbu bilah yang bergerak dari akar ke ujung) adalah kuncinya: bilah yang lebih pendek dan lebih bengkok akan menjadi bilah bertekanan tinggi, bilah yang lebih panjang dan lebih lurus akan menjadi bilah bertekanan rendah. Dua bilah dengan panjang yang sama dapat berasal dari satu tahap tekanan tinggi dan yang lainnya dari tahap tekanan rendah dari mesin yang berbeda: "pendek" dan "panjang" relatif terhadap ukuran mesin. Di sisi lain, kompresor radial dan turbin radial lebih sulit dibedakan.
Desain bilah turbin dan bilah kompresor, meskipun keduanya merupakan komponen penting dalam turbin gas dan mesin jet, berbeda secara signifikan karena fungsi dan kondisi pengoperasiannya yang berbeda. Berikut adalah rincian perbedaan utamanya:
- Fungsi
- Bilah Turbin: Bilah turbin mengekstraksi energi dari aliran gas bersuhu tinggi dan bertekanan tinggi. Bilah tersebut mengubah energi termal menjadi energi mekanis, yang menyebabkan turbin berputar dan menggerakkan kompresor atau menghasilkan kerja untuk berbagai aplikasi.
- Bilah Kompresor: Bilah kompresor, di sisi lain, dirancang untuk memampatkan udara atau gas yang masuk, meningkatkan tekanan dan suhunya sebelum memasuki ruang pembakaran. Proses ini mengharuskan bilah untuk memberikan energi ke gas.
- Aerodinamika
- Bilah Turbin: Desainnya berfokus pada pemaksimalan ekstraksi energi. Bilah tersebut sering kali dirancang dengan rasio aspek tinggi dan bentuk airfoil khusus yang mengoptimalkan aliran untuk konversi energi. Bilah tersebut harus menangani berbagai kondisi aliran, termasuk kecepatan tinggi dan turbulensi.
- Bilah Kompresor: Bilah ini dirancang untuk meningkatkan tekanan gas secara efisien. Biasanya, turbin memiliki sudut serang yang lebih agresif dan dibentuk untuk memastikan aliran udara yang lancar sekaligus meminimalkan kerugian. Desain ini mengutamakan stabilitas dan efisiensi pada berbagai laju aliran.
- Kondisi Pengoperasian
- Bilah Turbin: Turbin beroperasi di lingkungan bersuhu tinggi dan bertekanan tinggi, yang sering kali membutuhkan material yang dapat menahan kondisi ekstrem. Teknik pendinginan (seperti saluran pendingin internal) sering kali dimasukkan ke dalam desain untuk mencegah panas berlebih.
- Bilah Kompresor: Kompresor beroperasi pada suhu yang lebih rendah daripada turbin tetapi harus menangani tekanan tinggi. Desain harus memastikan bahwa bilah tidak macet dan dapat menangani aliran kompresibel secara efisien.
- Pemilihan Material
- Bilah Turbin: Material dipilih untuk ketahanan suhu tinggi, sering kali menggunakan paduan super yang mempertahankan kekuatan dan integritas dalam kondisi ekstrem. Pelapis permukaan juga dapat diterapkan untuk meningkatkan daya tahan terhadap oksidasi dan kelelahan termal.
- Bilah Kompresor: Material berfokus pada kekuatan dan sifat ringan, karena pengurangan berat sangat penting untuk kinerja. Paduan aluminium dan material komposit umum digunakan dalam aplikasi bertekanan rendah, sementara aplikasi berkinerja tinggi dapat menggunakan titanium atau baja.
- Geometri Bilah
- Bilah Turbin: Biasanya memiliki geometri yang kompleks, termasuk puntiran dan lancip variabel untuk mengoptimalkan aliran dan ekstraksi energi di sepanjang bilah. Bilah ini sering kali memiliki profil yang lebih melengkung.
- Bilah Kompresor: Bilah ini umumnya lebih seragam bentuknya, dengan kelengkungan yang lebih sedikit dibandingkan dengan bilah turbin. Desainnya sering kali mencakup fitur seperti jarak bebas ujung bilah dan selubung untuk mengendalikan aliran udara dan mencegah kehilangan.
Lingkungan dan mode kegagalan
Bilah turbin mengalami lingkungan yang sangat berat di dalam turbin gas. Bilah turbin menghadapi suhu tinggi, tekanan tinggi, dan lingkungan yang berpotensi bergetar tinggi. Ketiga faktor ini dapat menyebabkan kegagalan bilah turbin, yang berpotensi merusak mesin, oleh karena itu bilah turbin dirancang dengan cermat untuk menahan kondisi ini.[12]
Bilah turbin mengalami tekanan dari gaya sentrifugal (tahap turbin dapat berputar pada puluhan ribu putaran per menit (RPM)) dan gaya fluida yang dapat menyebabkan kegagalan fraktur, luluh, atau creep. Selain itu, tahap pertama (tahap langsung setelah pembakar) turbin gas modern menghadapi suhu sekitar 2.500 °F (1.370 °C), naik dari suhu sekitar 1.500 °F (820 °C) pada turbin gas awal. Mesin jet militer modern, seperti Snecma M88 , dapat melihat suhu turbin 2.900 °F (1.590 °C). Suhu tinggi tersebut dapat melemahkan bilah dan membuatnya lebih rentan terhadap kegagalan creep. Suhu tinggi juga dapat membuat bilah rentan terhadap kegagalan korosi. Terakhir, getaran dari mesin dan turbin itu sendiri dapat menyebabkan kegagalan kelelahan.
Bahan
Faktor pembatas pada mesin jet awal adalah kinerja bahan yang tersedia untuk bagian panas (pembakar dan turbin) mesin. Kebutuhan akan bahan yang lebih baik memacu banyak penelitian di bidang paduan dan teknik manufaktur, dan penelitian tersebut menghasilkan daftar panjang bahan dan metode baru yang memungkinkan turbin gas modern. Salah satu yang paling awal adalah Nimonic, yang digunakan dalam mesin Whittle Inggris.
Pengembangan superalloy pada tahun 1940-an dan metode pemrosesan baru seperti peleburan induksi vakum pada tahun 1950-an sangat meningkatkan kemampuan suhu bilah turbin. Metode pemrosesan lebih lanjut seperti pengepresan isostatik panas meningkatkan paduan yang digunakan untuk bilah turbin dan meningkatkan kinerja bilah turbin. Bilah turbin modern sering menggunakan superalloy berbasis nikel yang menggabungkan kromium, kobalt, dan renium.[13][14][15][16][17][18][19][20]
Selain perbaikan paduan, terobosan besar adalah pengembangan metode pemadatan terarah (DS) dan produksi kristal tunggal (SC). Metode ini sangat membantu meningkatkan kekuatan terhadap kelelahan dan creep dengan menyelaraskan batas butir dalam satu arah (DS) atau dengan menghilangkan batas butir sama sekali (SC). Penelitian SC dimulai pada tahun 1960-an dengan Pratt dan Whitney dan memakan waktu sekitar 10 tahun untuk diimplementasikan. Salah satu implementasi pertama DS adalah dengan mesin J58 dari SR-71.
Peningkatan besar lainnya pada teknologi bahan bilah turbin adalah pengembangan lapisan penghalang termal (TBC). Sementara pengembangan DS dan SC meningkatkan ketahanan terhadap creep dan kelelahan, TBC meningkatkan ketahanan terhadap korosi dan oksidasi, yang keduanya menjadi perhatian lebih besar saat suhu meningkat. TBC pertama, yang diterapkan pada tahun 1970-an, adalah lapisan aluminida . Lapisan keramik yang ditingkatkan mulai tersedia pada tahun 1980-an. Lapisan ini meningkatkan kemampuan suhu bilah turbin sekitar 200 °F (90 °C). Lapisan ini juga meningkatkan masa pakai bilah, hampir menggandakan masa pakai bilah turbin dalam beberapa kasus.
Sebagian besar bilah turbin diproduksi dengan pengecoran investasi (atau pemrosesan lilin yang hilang). Proses ini melibatkan pembuatan cetakan negatif yang presisi dari bentuk bilah yang diisi dengan lilin untuk membentuk bentuk bilah. Jika bilah berongga (yaitu, memiliki saluran pendingin internal), inti keramik dalam bentuk saluran tersebut dimasukkan ke tengah. Bilah lilin dilapisi dengan bahan tahan panas untuk membuat cangkang, dan kemudian cangkang tersebut diisi dengan paduan bilah. Langkah ini bisa lebih rumit untuk bahan DS atau SC, tetapi prosesnya serupa. Jika ada inti keramik di tengah bilah, inti tersebut dilarutkan dalam larutan yang membuat bilah berongga. Bilah dilapisi dengan TBC, dan kemudian lubang pendingin apa pun dikerjakan dengan mesin.
Komposit matriks keramik (CMC), di mana serat tertanam dalam matriks keramik yang berasal dari polimer, sedang dikembangkan untuk digunakan pada bilah turbin. Keuntungan utama CMC dibandingkan superalloy konvensional adalah bobotnya yang ringan dan kemampuan suhu tinggi. Komposit SiC/SiC yang terdiri dari matriks silikon karbida yang diperkuat oleh serat silikon karbida telah terbukti dapat menahan suhu operasi 200°-300 °F lebih tinggi daripada superalloy nikel. GE Aviation berhasil menunjukkan penggunaan bilah komposit SiC/SiC tersebut untuk turbin tekanan rendah dari mesin jet F414-nya.
Daftar bahan bilah turbin
Catatan: Daftar ini tidak mencakup semua paduan yang digunakan pada bilah turbin.
- U-500 Material ini digunakan sebagai material tahap pertama (tahap yang paling sulit) pada tahun 1960an, dan sekarang digunakan pada tahap selanjutnya yang tidak terlalu sulit.
- Rene 77
- Rene N5[21]
- Rene N6
- PWA1484
- CMSX-4 [22]
- CMSX-10
- Inconel
- IN-738 – GE menggunakan IN-738 sebagai bahan bilah tahap pertama dari tahun 1971 hingga 1984, saat digantikan oleh GTD-111. Sekarang digunakan sebagai bahan tahap kedua. Bahan ini secara khusus dirancang untuk turbin darat, bukan turbin gas pesawat terbang.
- GTD-111 Bilah terbuat dari GTD-111 yang dipadatkan secara terarah digunakan dalam banyak turbin gas GE Energy pada tahap pertama. Bilah yang terbuat dari GTD-111 yang dipadatkan secara ekuaksial digunakan pada tahap selanjutnya.
- EPM-102 (MX4 (GE), PWA 1497 (P&W)) adalah paduan super kristal tunggal yang dikembangkan bersama oleh NASA, GE Aviation, dan Pratt & Whitney untuk Transportasi Sipil Berkecepatan Tinggi (HSCT). Meskipun program HSCT dibatalkan, paduan tersebut masih dipertimbangkan untuk digunakan oleh GE dan P&W.[23]
- Nimonic 80a digunakan untuk bilah turbin pada Rolls-Royce Nene dan de Havilland Ghost
- Nimonic 90 digunakan pada Bristol Proteus.
- Nimonic 105 digunakan pada Rolls-Royce Spey.
- Nimonic 263 digunakan dalam ruang bakar Bristol Olympus yang digunakan pada pesawat supersonik Concorde.[24][25]
- 3D printed thermoplastic resin untuk membuat bilah turbin angin sedang dikembangkan melalui kemitraan antara ORNL, NREL, dan GE Renewable Energy.
Pendinginan







Pada rasio tekanan konstan, efisiensi termal mesin meningkat seiring dengan peningkatan suhu masuk turbin (TET). Akan tetapi, suhu tinggi dapat merusak turbin, karena bilah berada di bawah tekanan sentrifugal yang besar dan material lebih lemah pada suhu tinggi. Jadi, pendinginan bilah turbin sangat penting untuk tahap awal, tetapi karena suhu gas turun pada setiap tahap, hal ini tidak diperlukan untuk tahap selanjutnya seperti pada turbin tekanan rendah atau turbin daya. Desain turbin modern saat ini beroperasi dengan suhu masuk lebih tinggi dari 1900 kelvin yang dicapai dengan mendinginkan komponen turbin secara aktif.[26]
Metode pendinginan
Bilah turbin didinginkan menggunakan udara, kecuali untuk penggunaan terbatas pendinginan uap dalam pembangkit listrik siklus gabungan. Pendinginan air telah diuji secara ekstensif tetapi belum pernah diperkenalkan. Turbin gas kelas "H" General Electric telah mendinginkan bilah berputar dan baling-baling statis menggunakan uap dari turbin uap siklus gabungan meskipun GE dilaporkan pada tahun 2012 akan kembali ke pendinginan udara untuk unit "FlexEfficiency" nya. Pendinginan cair tampaknya lebih menarik karena kapasitas panas spesifik yang tinggi dan kemungkinan pendinginan evaporatif tetapi dapat terjadi kebocoran, korosi, tersedak dan masalah lain yang bekerja melawan metode ini. Di sisi lain, pendinginan udara memungkinkan udara yang dikeluarkan ke aliran utama tanpa masalah. Kuantitas udara yang dibutuhkan untuk tujuan ini adalah 1-3% dari aliran utama dan suhu bilah dapat dikurangi hingga 200-300 °C. Ada banyak teknik pendinginan yang digunakan dalam bilah turbin gas; konveksi , film, pendinginan transpirasi, pendinginan efusi, pendinginan sirip pin, dll. yang termasuk dalam kategori pendinginan internal dan eksternal. Meskipun semua metode memiliki perbedaan, semuanya bekerja dengan menggunakan udara dingin yang diambil dari kompresor untuk menghilangkan panas dari bilah turbin.[27][28]
Pendinginan internal
Pendinginan konveksi

Ia bekerja dengan melewatkan udara pendingin melalui saluran internal ke bilah. Panas dipindahkan melalui konduksi melalui bilah, dan kemudian melalui konveksi ke udara yang mengalir di dalam bilah. Luas permukaan internal yang besar diinginkan untuk metode ini, sehingga jalur pendinginan cenderung berkelok-kelok dan penuh sirip kecil. Saluran internal di bilah mungkin berbentuk lingkaran atau elips. Pendinginan dicapai dengan melewatkan udara melalui saluran ini dari hub menuju ujung bilah. Udara pendingin ini berasal dari kompresor udara. Dalam kasus turbin gas, fluida di luar relatif panas yang melewati saluran pendingin dan bercampur dengan aliran utama di ujung bilah.[29]
Pendinginan benturan

Variasi pendinginan konveksi, pendinginan benturan, bekerja dengan menghantam permukaan bagian dalam bilah dengan udara berkecepatan tinggi. Hal ini memungkinkan lebih banyak panas yang ditransfer melalui konveksi daripada pendinginan konveksi biasa. Pendinginan benturan digunakan di wilayah dengan beban panas terbesar. Dalam kasus bilah turbin, tepi depan memiliki suhu maksimum dan dengan demikian beban panas. Pendinginan benturan juga digunakan di bagian tengah tali bilah. Bilah berongga dengan inti. Ada saluran pendingin internal. Udara pendingin masuk dari wilayah tepi depan dan berputar ke arah tepi belakang.
Pendinginan eksternal
Pendinginan film

Pendinginan film (juga disebut pendinginan film tipis), jenis yang digunakan secara luas, memungkinkan efektivitas pendinginan yang lebih tinggi daripada pendinginan konveksi dan benturan. Teknik ini terdiri dari memompa udara pendingin keluar dari bilah melalui beberapa lubang atau slot kecil dalam struktur. Lapisan tipis (film) udara pendingin kemudian dibuat pada permukaan luar bilah, mengurangi perpindahan panas dari aliran utama, yang suhunya (1300–1800 kelvin) dapat melebihi titik leleh bahan bilah (1300–1400 kelvin). Kemampuan sistem pendingin film untuk mendinginkan permukaan biasanya dievaluasi menggunakan parameter yang disebut efektivitas pendinginan. Efektivitas pendinginan yang lebih tinggi (dengan nilai maksimum satu) menunjukkan bahwa suhu bahan bilah lebih dekat ke suhu pendingin. Di lokasi di mana suhu bilah mendekati suhu gas panas, efektivitas pendinginan mendekati nol. Efektivitas pendinginan terutama dipengaruhi oleh parameter aliran pendingin dan geometri injeksi. Parameter aliran pendingin meliputi rasio kecepatan, kepadatan, hembusan, dan momentum yang dihitung menggunakan karakteristik aliran pendingin dan aliran utama. Parameter geometri injeksi terdiri dari geometri lubang atau celah (yaitu lubang atau celah berbentuk silinder) dan sudut injeksi. Sebuah program Angkatan Udara Amerika Serikat pada awal tahun 1970-an mendanai pengembangan bilah turbin yang didinginkan dengan film dan konveksi, dan metode tersebut telah menjadi umum pada bilah turbin modern.
Menyuntikkan cairan pendingin ke dalam aliran mengurangi efisiensi isentropik turbin; kompresi udara pendingin (yang tidak memberikan daya ke mesin) menimbulkan penalti energi; dan sirkuit pendingin menambahkan kompleksitas yang cukup besar ke mesin.Semua faktor ini harus dikompensasi dengan peningkatan kinerja keseluruhan (daya dan efisiensi) yang dimungkinkan oleh peningkatan suhu turbin.[30][31][32][33][34][35]
Dalam beberapa tahun terakhir, para peneliti telah menyarankan penggunaan aktuator plasma untuk pendinginan film. Pendinginan film bilah turbin dengan menggunakan aktuator plasma pelepasan penghalang dielektrik pertama kali diusulkan oleh Roy dan Wang. Aktuator plasma berbentuk tapal kuda, yang dipasang di sekitar lubang untuk aliran gas, telah terbukti meningkatkan efektivitas pendinginan film secara signifikan. Mengikuti penelitian sebelumnya, laporan terbaru menggunakan metode eksperimental dan numerik menunjukkan efek peningkatan pendinginan sebesar 15% menggunakan aktuator plasma.[36][37] [38]
Efusi pendingin

Permukaan bilah terbuat dari bahan berpori yang berarti memiliki sejumlah besar lubang kecil di permukaannya. Udara pendingin dipaksa melalui lubang-lubang berpori ini yang membentuk lapisan film atau lapisan batas pendingin. Selain itu, pendinginan yang seragam disebabkan oleh efusi pendingin ke seluruh permukaan bilah.
Pendinginan sirip pin
Pada tepi belakang yang sempit, pendinginan film digunakan untuk meningkatkan perpindahan panas dari bilah. Ada serangkaian sirip pin pada permukaan bilah. Perpindahan panas terjadi dari serangkaian ini dan melalui dinding samping. Saat pendingin mengalir melintasi sirip dengan kecepatan tinggi, aliran tersebut terpisah dan terbentuklah pusaran. Banyak faktor yang berkontribusi terhadap laju perpindahan panas, di antaranya jenis sirip pin dan jarak antar sirip merupakan faktor yang paling signifikan.[39]
Pendinginan transpirasi
Ini mirip dengan pendinginan film karena menciptakan lapisan tipis udara pendingin pada bilah, tetapi berbeda karena udara "bocor" melalui cangkang berpori daripada disuntikkan melalui lubang. Jenis pendinginan ini efektif pada suhu tinggi karena secara merata menutupi seluruh bilah dengan udara dingin. Bilah yang didinginkan transpirasi umumnya terdiri dari penyangga kaku dengan cangkang berpori. Udara mengalir melalui saluran internal penyangga dan kemudian melewati cangkang berpori untuk mendinginkan bilah. Seperti halnya pendinginan film, peningkatan udara pendingin menurunkan efisiensi turbin, oleh karena itu penurunan tersebut harus diimbangi dengan peningkatan kinerja suhu.
Lihat pula
- Kompresor (pemampat)
- Desain perhitungan kipas aksial
- Gaya (fisika)
- Daya
- Laju
- Tekanan
- Efisiensi energi
- Mesin jet
- Turbojet
- Turbofan
- Propfan
- Turboshaft
- Turboprop
- Turbin gas
- Mesin reaksi
- Baling-baling
- Baling-baling pesawat
Referensi

- ^ The Cambridge Aerospace Dictionary, Bill Gunston,ISBN 0 511 33833 3
- ^ "Plastic blades for gas turbine engines".
- ^ Acharya, Sumanta; Kanani, Yousef (2017-01-01), Sparrow, Ephraim M.; Abraham, John P.; Gorman, John M. (ed.), "Chapter Three - Advances in Film Cooling Heat Transfer", Advances in Heat Transfer, vol. 49, Elsevier, hlm. 91–156, doi:10.1016/bs.aiht.2017.10.001, diakses tanggal 2019-08-30
- ^ Goldstein, Richard J. (1971-01-01), "Film Cooling", dalam Irvine, Thomas F.; Hartnett, James P. (ed.), Advances in Heat Transfer Volume 7, vol. 7, Elsevier, hlm. 321–379, doi:10.1016/s0065-2717(08)70020-0, ISBN 9780120200078, diakses tanggal 2019-08-30
- ^ Bogard, D. G.; Thole, K. A. (2006-03-01). "Gas Turbine Film Cooling" (PDF). Journal of Propulsion and Power. 22 (2): 249–270. doi:10.2514/1.18034. S2CID 54063370. Diarsipkan dari asli (PDF) tanggal 2019-03-07.
- ^ https://alliedpg.com/latest-articles/types-of-coatings-for-gas-turbine-blades/
- ^ Wang, Wen; Yan, Yan; Zhou, Yeqi; Cui, Jiahuan (2022). "Review of Advanced Effusive Cooling for Gas Turbine Blades". Energies. 15 (22): 8568. doi:10.3390/en15228568.
- ^ Bhagi LK, Rastogi V, Gupta P (2017). "Study of corrosive fatigue and life enhancement of low pressure steam turbine blade using friction dampers". Journal of Mechanical Science and Technology. 31: 17–27. doi:10.1007/s12206-016-1203-5. S2CID 115023151.
- ^ https://www.researchgate.net/publication/267620184_Fundamental_Differences_Between_Conventional_and_Geared_Turbofans, Fig.1.5-14
- ^ https://www.yumpu.com/en/document/read/11154551/geared-fan-vki-aero-engine-design-mtu-aero-engines, p.15
- ^ Bhagi LK, Rastogi V, Gupta P (2013).Fractographic investigations of the failure of L-1 low pressure steam turbine blade. Case Studies in Engineering Failure Analysis, 1(2), pp.72–78
- ^ Dexclaux, Jacques and Serre, Jacque (2003). "M88-2 E4: Advanced New Generation Engine for Rafale Multirole Fighter". AIAA/ICAS International Air and Space Symposium and Exposition: The Next 100 Years. 14–17 July 2003, Dayton, Ohio. AIAA 2003-2610
- ^ Koff, Bernard L. (2003). "Gas Turbine Technology Overview – A Designer's Perspective". AIAA/ICAS International Air and Space Symposium and Exposition: The Next 100 Years. 14–17 July 2003, Dayton, Ohio. AIAA 2003-2722.
- ^ Magyar, Michael J. "Mineral Yearbook: Rhenium" (PDF). United States Geological Survey.
- ^ Langston, Lee S. (16 March 2018). "Single-Crystal Turbine Blades Earn ASME Milestone Status". www.machinedesign.com. Diakses tanggal 25 November 2018.
- ^ Langston, Lee S. (6 February 2017). "Each Blade a Single Crystal". www.americanscientist.org. Diakses tanggal 25 November 2018.
- ^ Takeshi, Takashi, Kuniyuki, Ken-ichi, Masato. "Development of CMC Turbine Parts for Aero Engines" (PDF). Pemeliharaan CS1: Banyak nama: authors list (link)
- ^ Halbig, Jaskowiak, Kiser, Zhu (June 2013). "Evaluation of Ceramic Matrix Composite Technology for Aircraft Turbine Engine Applications" (PDF). 51st AIAA Aerospace Sciences Meeting Including the New Horizons Forum and Aerospace Exposition. doi:10.2514/6.2013-539. hdl:2060/20130010774. ISBN 978-1-62410-181-6. Pemeliharaan CS1: Banyak nama: authors list (link)
- ^ "Ceramic Matrix Composites Allow GE Jet Engines to Fly Longer – GE Reports". GE Reports. 9 February 2015. Diakses tanggal 2 November 2015.
- ^ "GE Successfully Tests World's First Rotating Ceramic Matrix Composite Material for Next-Gen Combat Engine | Press Release | GE Aviation". www.geaviation.com. Diakses tanggal 2 November 2015.
- ^ MacKay, Rebecca A., et al. (2007). Low-Density, Creep-Resistant Superalloys Developed for Turbine Blades. NASA Glenn's Research & Technology. Updated: 7 November 2007. Retrieved: 16 June 2010.
- ^ P. Caron, Y. Ohta, Y.G. Nakagawa, T. Khan (1988): Superalloys 1988 (edited by S. Reichmann et al.), p. 215. The Metallurgical Society of AIME, Warrendale, PA.
- ^ S. Walston, A. Cetel, R. MacKay, K. O’Hara, D. Duhl, and R. Dreshfield (2004). Joint Development of a Fourth Generation Single Crystal Superalloy Diarsipkan 15 October 2006 di Wayback Machine.. NASA TM—2004-213062. December 2004. Retrieved: 16 June 2010.
- ^ "Metal Tidbits: Nimonic." steelforge.com. Retrieved: 5 March 2011.
- ^ "Products." Diarsipkan 8 December 2012 di Archive.is Special Metals. Retrieved: 5 March 2011.
- ^ Yahya, S M (2011). Turbines Compressors and Fans. New delhi: Tata McGraw-Hill Education, 2010. hlm. 430–433. ISBN 9780070707023.
- ^ Gas Turbine Engineering Handbook Second Edition, Boyce, ISBN 0 88415 732 6, Fig. 9-23 General Electric "Water-cooled turbine blade"
- ^ "Moving beyond the steam cooling". 13 February 2012.
- ^ "Hollow, air cooled turbine blades".
- ^ Volume 1. Performance Flight Testing Phase. Chapter 7. Aero Propulsion page 7.122. Edwards Air Force Base, Air Force Test Center, February 1991. Size: 8MB. mirror of ADA320315.pdf
- ^ What is Film Cooling?
- ^ Martinez, Isidoro. "Aircraft propulsion. Thermal and mechanical limitations in jet engines Diarsipkan 2015-07-01 di Wayback Machine." page 19. Technical University of Madrid, School of Aeronautical Engineering, 2015. Retrieved: April 2015.
- ^ Rolls-Royce plc (2005). The Jet Engine (Edisi 6). Rolls-Royce plc. ISBN 978-0902121232.
- ^ Boyce, p. 379-80
- ^ S. Roy, C.-C. Wang, Plasma actuated heat transfer, Appl. Phys. Lett. 92 (2008) 231501
- ^ P. Audier, M., N. Benard, E. Moreau, Film cooling effectiveness enhancement using surface dielectric barrier discharge plasma actuator, Int. J. Heat Fluid Flow 62 (2016), 247–57.
- ^ S. Dai, Y. Xiao, L. He, T. Jin, P. Hou, Q. Zhang, Z. Zhao, Computational study of plasma actuator on film cooling performance for different shaped holes, AIP Adv. 5 (2015), 067104.
- ^ Y. Xiao, S. Dai, L. He, T. Jin, Q. Zhang, P. Hou, Investigation of film cooling from cylindrical hole with plasma actuator on flat plate, Heat Mass Transf. 52 (2016), 1571–83.
- ^ Lesley M. Wright, Je-Chin Han. "Enhanced Internal Cooling of Turbine Blades and Vanes". 4.2.2.2 Enhanced Internal Coolingof Turbine Blades and Vanes. Diakses tanggal 27 May 2013.
- YAHYA, SM (2011). "Chapter 10: High temperature(cooled) turbine stages". turbines, compressor and fans (Edisi 4th). New delhi: Tata McGraw Hill Education private limited. ISBN 978-0-07-070702-3.
- Flack, Ronald D. (2005). "Chapter 8: Axial Flow Turbines". Fundamentals of Jet Propulsion with Applications. Cambridge Aerospace Series. New York, NY: Cambridge University Press. ISBN 978-0-521-81983-1.
- Boyce, Meherwan P. (2006). "Chapter 9: Axial Flow Turbines and Chapter 11: Materials". Gas Turbine Engineering Handbook (Edisi 3rd). Oxford: Elsevier. ISBN 978-0-7506-7846-9.
Pranala luar
- http://www.power-technology.com/ WIROMET - Steam Turbine Blades and Steam Flow System Parts
- http://www.arcam.com/ EBM® in Aerospace Diarsipkan 2013-10-25 di Wayback Machine.
- http://www.itclips.net/ Single Crystal Superalloys[pranala nonaktif permanen]
- http://www.cblade.it/ Steam Turbine Blades
- http://www.svhitechind.com/ Shri Venkateshwara Hi-Tech Industries[pranala nonaktif permanen]
- http://www.stork-gears.com/ Turbine Blade Manufacturer Stork H&E Turbo Blading
- http://www.turbocare.com/ Gas Turbine Blades and Buckets[pranala nonaktif permanen]
- Video
- http://www.youtube.com/ How It's Made- jet turbine blades
- http://www.youtube.com/ Jet Engine "Turbine Blade Fabrication" circa 1955 NACA 5min
- http://www.youtube.com/ How Do They Do It: Jet Engines
- http://www.youtube.com/ How Its Made Jet Compressor Blades
- http://www.youtube.com/ Air-Cooled Blades - Turbine Engines: A Closer Look